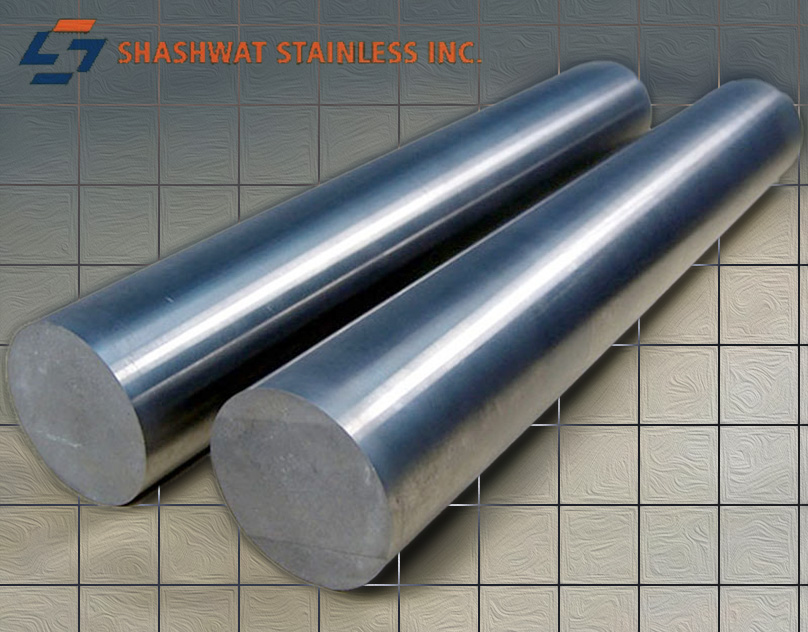
Round bars are essential components of manufacturing, engineering, and building processes and are utilized extensively in a wide range of sectors. Shashwat Stainless Inc. is the Top Quality Round Bars Manufacturer in India. These cylindrical metal bars, which are extremely resilient and versatile, play a major role in providing structural stability and support. This article’s goal is to provide a comprehensive analysis of the key factors influencing round bars, with a focus on material selection, manufacturing processes, and application-specific issues.
Material Selection: The Backbone of Round Bar Performance
The choice of material has a big impact on round bars’ properties and functionality. Typical materials include carbon steel, alloy steel, aluminum, and stainless steel. Each material possesses a unique set of properties that qualify it for a particular set of applications.
Carbon Steel:
Round carbon steel bars are employed in typical engineering and building projects because of their high tensile strength and affordable cost. However, because they may be prone to corrosion, they are not recommended for use in environments with high moisture content or corrosive substances.
Alloy Steel:
Because alloy steel round bars are more resilient to abrasion, stronger, and longer-lasting than other materials, they are the material of choice for demanding applications requiring optimal performance. However, as a trade-off, the cost is greater than with carbon steel.
Stainless Steel:
Round stainless steel bars have a high value because of their attractive appearance and resistance to corrosion. These bars are suitable for use in architectural projects, nautical applications, and the food industry. They are widely used when there is an issue with moisture or chemical exposure. The drawback is a higher initial cost.
Aluminum:
Because of their well-known lightweight and corrosion resistance, aluminum round bars are ideal for usage in the automotive, aerospace, and marine sectors. They could not be as sturdy as their steel counterparts, thus the specifics of the project need to be carefully considered.
Manufacturing Processes: Shaping Round Bars for Optimal Performance
Round bar quality and consistency are mostly dictated by the manufacturing process. Each of the two primary methods—hot rolling and cold drawing—has pros and cons of its own.
Hot Rolling:
The metal is heated to a high temperature and then run through rollers to take on the proper shape. Because hot-rolled round bars often have excellent mechanical properties, they are useful in situations where strength and durability are crucial. However, the surface polish may be less precise than that of cold-drawn bars.
Cold Drawing:
Cold-drawn round bars are produced by pulling metal through a die at room temperature, which results in improved dimensional tolerances and a smoother surface finish. While the surface quality of cold-drawn bars may be superior, their strength may not match that of their hot-rolled equivalents.
Tradeoffs in Material and Manufacturing: Striking the Right Balance
The right manufacturing technique must be balanced with the properties of the material to produce the perfect round bar. Engineers and project managers need to carefully assess the specific requirements of its use, taking into consideration factors like corrosion resistance, cost-effectiveness, and load-bearing capacity.
Application-Specific Considerations: Tailoring Round Bars to Unique Needs
Various businesses require round bars with particular properties suited to their needs. For instance:
Construction:
In building structures, the focus may be on high tensile strength and load-bearing capacity, making carbon or alloy steel round bars suitable choices.
Aerospace:
Lightweight aluminum round bars with corrosion resistance are crucial for applications in the aerospace industry, where fuel efficiency is a priority.
Food Industry:
Stainless steel round bars with excellent corrosion resistance are indispensable in the food industry, where hygiene and durability are paramount.
Challenges and Considerations: Navigating the Complexities of Round Bar Selection
Despite the myriad benefits of round bars, challenges and considerations arise in the decision-making process. These include:
Cost:
The initial cost and long-term maintenance expenses associated with round bars must be carefully evaluated against the budget constraints of a project.
Environmental Factors:
Consideration of the environmental conditions, including temperature, humidity, and exposure to corrosive elements, is crucial in selecting the most appropriate material.
Precision Requirements:
Some applications, such as precision machinery, may require round bars with tight dimensional tolerances, influencing the choice between hot rolling and cold drawing.
Environmental Impact: The Hidden Cost of Round Bars
In an era where environmental concerns are growing, it is imperative to consider how round bar selection affects the environment. The environmental impact of round bars should be considered in relation to their manufacturing energy consumption, overall carbon footprint, and possibilities for recycling.
Top Quality Round Bar Manufacturer in India
Shashwat Stainless Inc. is the Top Quality Round Bars Manufacturer in India. We are an ISO 9001:2008 certified company. Incepted in 2007, Shashwat Stainless Inc is promoted by a group of highly experienced technical personnel with rich experience in the manufacturing of Duplex Steel & Super Duplex Steel, Buttweld Fittings, Forged Fittings & Flanges.
Super Duplex Steel 32760 Round Bars Manufacturers
Super Duplex Steel 32750 Round Bars Manufacturers
SMO 254 F44 Round Bars Manufacturers
SMO 254 31254 Round Bars Manufacturers
17-4 ph Gr 630 Round Bars Manufacturers
17-4 ph S17400 Round Bars Manufacturers
Conclusion
The selection of round bars is a complicated process that requires careful consideration of the requirements specific to the application, manufacturing processes, and material properties. A project needs to strike the right balance between strength, cost, and environmental impact in order to be successful. Engineers and decision-makers have to traverse the complexity of selecting round bars, taking into consideration the trade-offs and challenges associated with different solutions. As industries continue to develop, it is becoming more and more crucial to make sustainable decisions about round bars in order to establish a robust and responsible future.